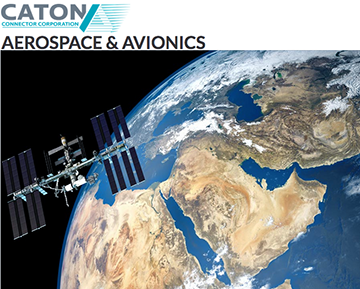
The U.S. Air Force and a leading defense contractor have tapped Caton Connector Corporation to supply high-voltage connectors and cable assemblies for an exceptionally demanding mission-critical application: the Milstar Satellite Communications System.
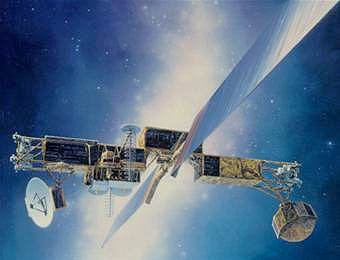
Artistic rendition of U.S.A.F.'s Milstar satellite.
The mission of Milstar, according to the U.S. Air Force, is to provide “the President, Secretary of Defense, and the U.S. armed forces with assured, survivable satellite communications (SATCOM) with low probability of interception and detection. Designed to overcome enemy jamming and nuclear effects, Milstar is the most robust and reliable SATCOM system currently employed by the Department of Defense (DoD).”
Caton was charged with designing and manufacturing high-voltage power-supply cables for various aspects of Milstar. They faced significant challenges and a daunting quality assurance and testing process. One of the most challenging aspects of the program was testing for the vacuum of space. The cables were required to withstand continuous use at 50,000 feet at temperatures of -55º Celsius. While the design of the MILSTAR connectors and cables was simple, the manufacturing process required extraordinary attention to detail.
Caton’s high-voltage in-house testing facility was custom designed to handle most any high-voltage testing requirement. The lab is so fully equipped that other manufacturers and universities sometime lease it to conduct their own tests. After successful validation, Caton’s high-voltage connectors and cables were used to power Milstar and are actively enabling its mission from orbit.
“We overcame multiple challenges during the design phase,” says Keith Rooney, Caton’s Milstar project lead. “Designing the cables was straightforward. However, the customer’s voltage requirement kept being raised after the design was completed. This increased demand on manufacturing time and tolerances. The company managed to keep the design and testing program unchanged while meeting the increased voltage requirement. Caton employed its patented no-corona, high-voltage connector technology that the firm developed in the 1980s in order to meet demanding military applications.
Testing MILSTAR put the lab through its paces. Rooney described the challenges of testing this satellite component and said that testing at simulated 50,000ʹ altitude while at -55°C is extremely difficult. The temperature alone is at the hairy edge for brittleness of silicone. Due to material shrinkage at that temperature, any slight misalignment or the connector not being fully mated could cause the cable assembly to fail at the interface. At that altitude, a void or air gap is expanded, and the voltage required to bridge that gap becomes sufficiently less, making this test extremely difficult. Additionally, tight tolerances mean that parts were methodically made. There was no rushing these parts. Every piece took as much time as necessary to ensure quality and pass testing. Each connector lead needed to be tested to ground and to each other. This need further increased the difficulty of testing.